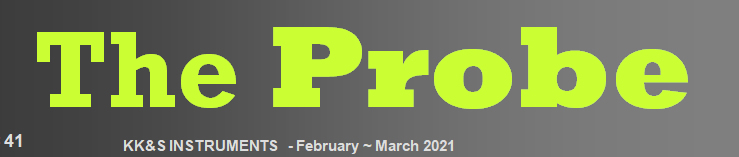
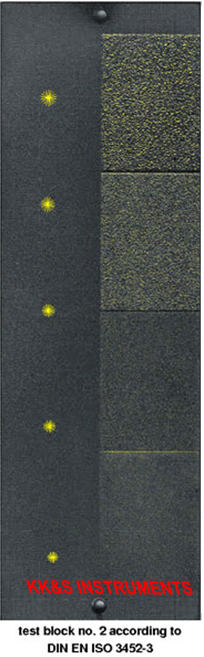
Penetrant Test Blocks According to ISO 3452.3
-
Test Block Type 2 – 4 test areas
-
Test panel Type 1 – 10μm Crack
-
Test panel Type 1 – 20μm Crack
-
Test panel Type 1 – 30μm Crack
-
Test panel Type 1 – 50μm Crack
-
Aluminium Comparator Block
to ASME Code V & ISO 3452-5 & -6
In This Issue:
- Cover – PT – Penetrant Test Block.
- News – From the Sales Desk – Institute Dr Foerster,
- = Demagnetization the pulse method – ZMAG CM CM.
- New member of the EMAG family: – EMAG K
- Special – 10% OFF – PT Type 2 Test Plate.
- Application – Military Equip. Inspection for Magnetic Signatures
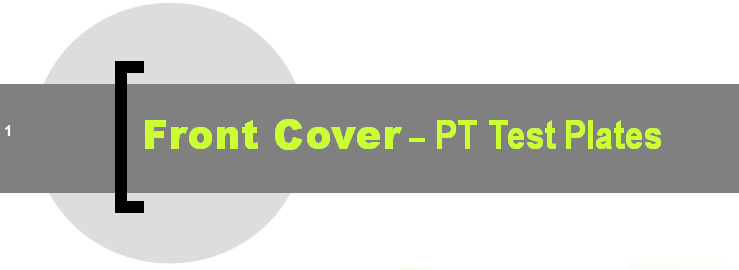
Reference test blocks for penetrant testing
For colour penetrant testing three main types of reference test blocks are available, each based on the applicable standard. We offer this selection of reference test blocks and are pleased to help you with supply.
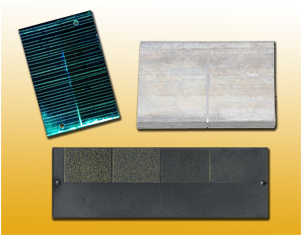
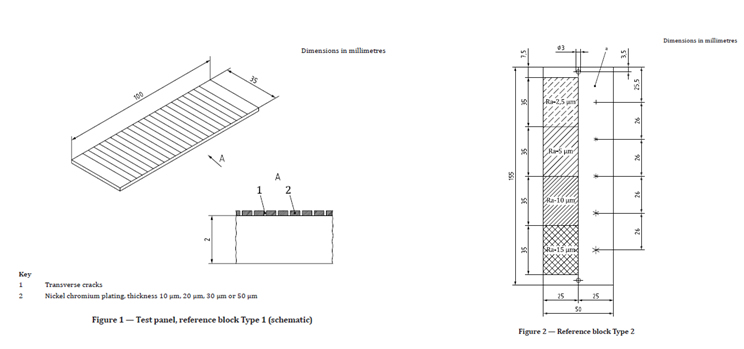
The Type 1; Reference block, nickel-chrome plated panels with 10 μm, 20 μm, 30 μm & 50 μm thickness of plating, respectively. These panels can be used for determination of the sensitivity of fluorescent penetrant systems. The sensitivity of colour contrast penetrant systems is determined using the 30 μm and 50 μm panels.
The Type 2; Reference block consists of a single panel of which one half has been plated with Electroless nickel and a thin layer of chromium and the other half prepared to achieve areas of specific roughness. The plated side exhibits five star-shaped discontinuities.
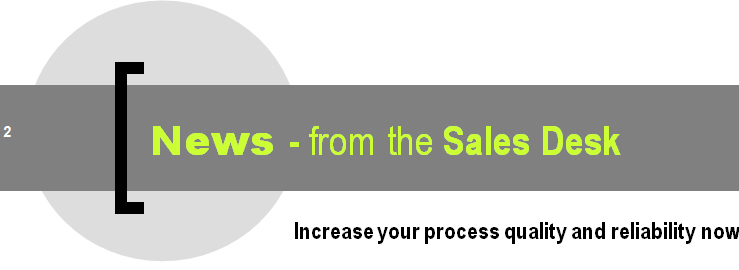
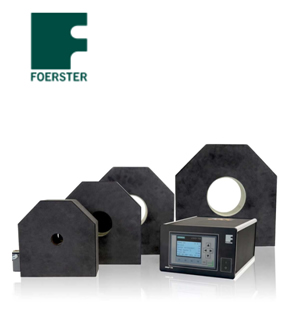
Increase your process quality and reliability now
Effective demagnetization via the pulse method – ZMAG
Magnetized components can lead to interference signals during crack or microstructure testing with eddy current. False results from the component condition and the associated pseudo rejects are the consequences.
To avoid this, offers you an appropriate solution: the powerful demagnetization unit ZMAG CM CM
Advantages: plug and play, pulse method, high demagnetization performance, flexible coil size, can be automated.
Technology: The pulse method – The ZMAG CM CM magnetization unit is operated with the pulse method. An approach that uses an alternating current pulse that flows through an appropriate coil. As a result, an alternating magnetic field that corresponds to the current is generated.
Integrated Solutions: STATOGRAPH & MAGNATEST offer results for; Elimination of Interference, Coating Process, MPI, Magnetic adhesion & Compliance to specification.
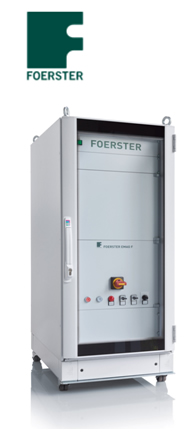
Foerster’s new member of the EMAG family: – EMAG K.
Various acceptance specification for semi-finished products demand items have their residual field strength below a stipulated value. The FOERSTER demagnetizers EMAG E, M and F specifically generate strong alternating magnetic fields which are proven to demagnetize such items.
UPDATE: The NEW EMAG K will replace the existing EMAG F, their powerful demagnetization device.
What are the upgrades?
New with the EMAG K there is an upgraded power supply, with these advantages:
– Coil current adjustable over a wider range with finer increments.
– More flexible adjustment of the coil current to compensate for interference fields.
– Lower demagnetization frequencies for higher penetration depths.
Another highlight is the design of the new power supply, It’s completely encapsulated to enhance Protection and Longevity
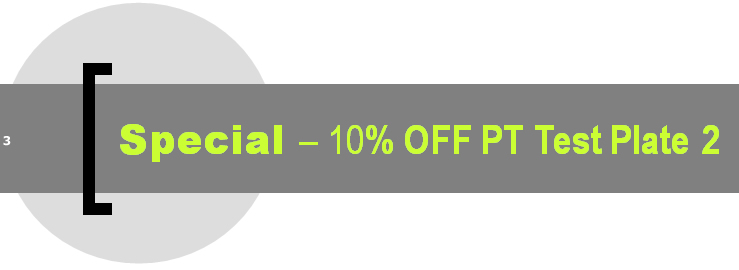
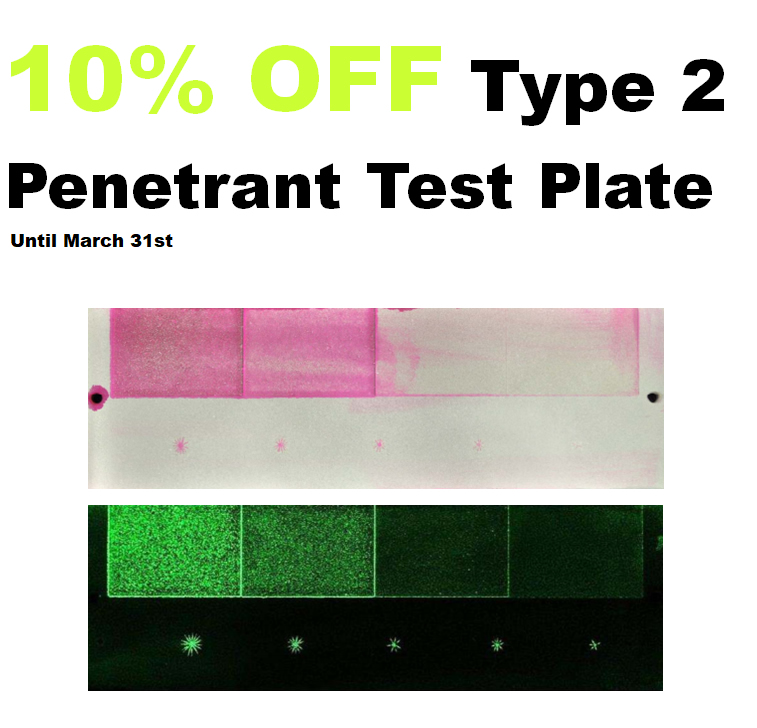
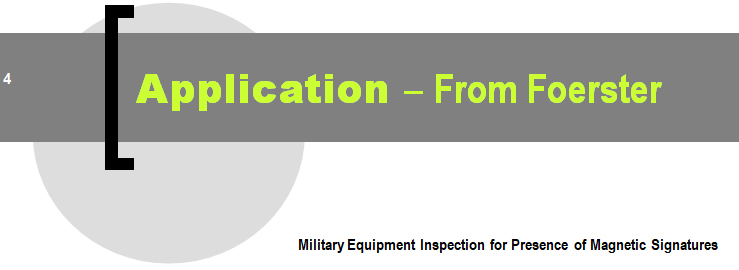
Industry: Defence
Material/Part type: Military equipment
Measuring parameter: Magnetic fi eld
Industry norm: STANAG 2897, AEODP-07
FOERSTER device: MAGNETOMAT & Differential Probe
Navy mine divers have to rely on non-magnetic explosive ordnance disposal equipment in order to be able to approach closely to a magnetically fused mine. The regular inspection of the equipment for a magnetic signature is indispensable part of demining preparation phase. The importance of this inspection is backed by various military standards, such as STANAG 2897 and AEODP-07.
Typically, explosive ordnance disposal (EOD) equipment comprises both diving equipment and further tools and fixtures which are planned to be used and placed in direct contact to the mines.
A couple of examples of such equipment are:
- EOD demining tools (e.g. hand and power tools.)
- Underwater breathing apparatus
- Ordnance locators
- Personal protective suits, helmets, visors
- Remotely operated vehicles
- Communication equipment
For that reason, the equipment and the material is made of respectively must demonstrate very poor magnetic properties, in other words they shall be “non-magnetic”. The detailed description of acceptable magnetic signature limits and requirements on inspection procedure setup is subject to STANAG 2897 and AEODP-07 standards. These norms are not only a guideline for inspection teams, but also for manufacturers of the corresponding diving equipment and tools.
Particularly, the above standards provide the firm limit for the total magnetic field signature of the specimen, which is set to 5 nT at the 10 cm distance from the tested object.
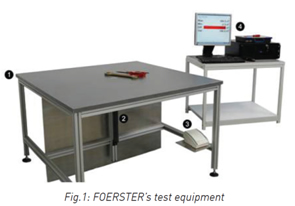
To address these specifications and Navy requirements FOERSTER has developed an effective testing solution (Fig. 1), which includes:
- Non-magnetic table, with adjustable probe mount
- Single axis differential probe, @ 200mm spacing
- Sensor electronic 100 μT Laboratory
- MAGNETOMAT, PC, with HotSpot Software
The above solution enables customers to measure nonmagnetic components rapidly and with high precision. Thanks to the differential probe and the non-magnetic table it is possible to limit the impact of unnecessary magnetic disturbances (e.g. earth magnetic field, side environmental magnetic impurities) in the process of inspection.
For magnetic signatures up to 5 nT on EOD equipment we recommend testing with FOERSTER’s MAGNETOMAT with Differential Probe and HotSpot Software. For more detailed information please contact: www.kks.com.au